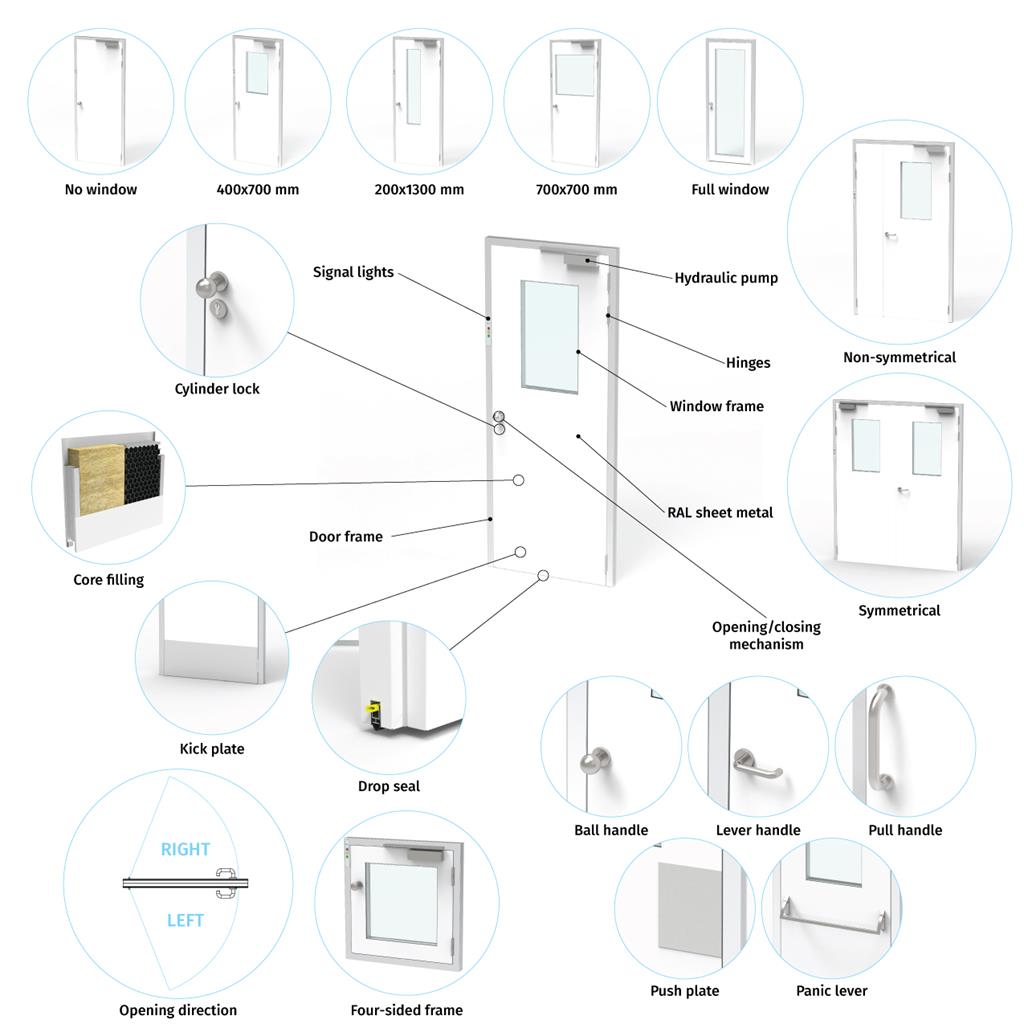
Door Configurator in Autodesk Inventor
The door configurator was created to standardize doors, and to make it easier for the sales department and the Project Office to select and define the doors. The door as a product has not been well defined and a change was necessary to achieve a faster response to the market demands and increased volume of work. This change meant, firstly, redefining the product as such and introducing new rules when choosing the types, options, and dimensions for the product. In addition, the configurator has greatly facilitated the process of generating production documentation, while also accelerating it. This has ultimately resulted in faster execution of inquiries and production orders.
The configurator is designed in such a way that the existing data, from the department that defines the door for the construction department, are used for data input, such as the door type, options and dimensions. Specifically, these are the CR development and CR preparation departments. Within their process, they generate Excel spreadsheets defining the door. The configurator uses this table as a database of sorts from which the data is automatically retrieved. After that, with a couple of mouse clicks, the process basically takes place automatically. According to the obtained input, a 3D model, drawing and DXF (i.e., the process output) are automatically generated with a couple of mouse clicks. It should be noted that the input data can also be entered manually into the configurator in case an Excel table is missing.
The configurator was developed within the Autodesk 3D software - Inventor on the iLogic platform, which is the "out of the box" feature of the functional software. Autodesk Vault PDM software is used to manage the configurator’s CAD data / output.
The operation of the configurator is explained in detail below.
The configurator works in the following way:
1. The department in charge of production preparation creates a table and its data are used for the door construction (door type, dimensions, options, etc.).
2. In Inventor, a window opens where a row from the above-mentioned table is selected. If there is no table from the preparation department, then the individual options can be selected by clicking on the drop-down menus in the configurator.
3. After approximately 1 minute, Inventor finishes modelling the positions that are variable depending on the model and the data it imported from the Excel spreadsheet.
4. The next step is to open the drawing - the new descriptions are automatically generated on it.
5. After opening and closing the drawing, the inventor sends the models to Vault (PDM software).
6. After saving the model and the drawing in Vault, changing the status of these files from "Work in Progress" to "Realized" automatically generates all DXF and PDF files that are further needed for production. CNC programmers use DXFs as the basis for creating CNC programs, and PDFs are used in production to bend, control, and assemble the final product.